Amphenol Aerospace Features & Technologies
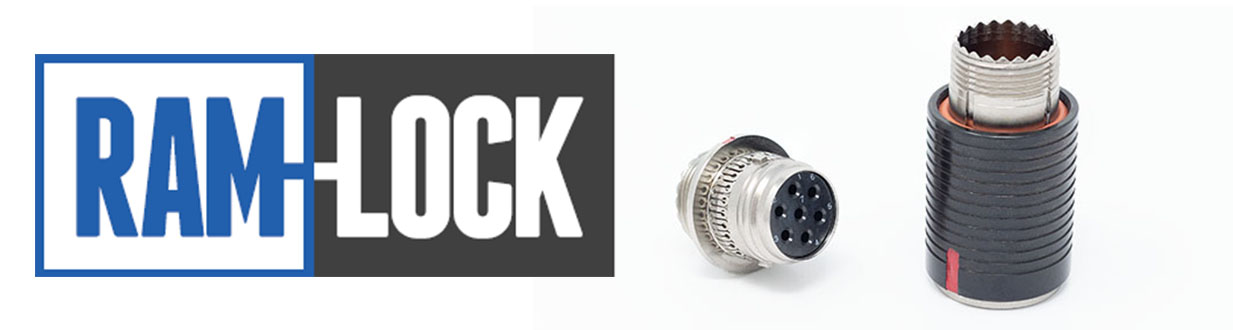
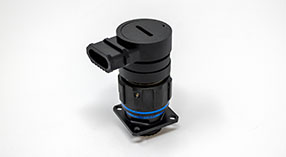
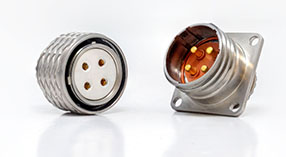
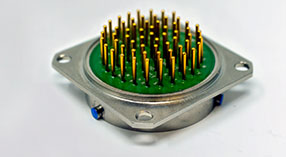
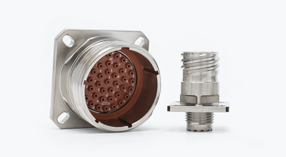
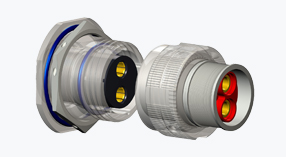
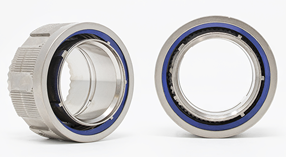
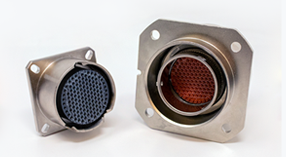
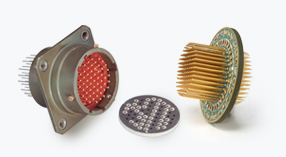
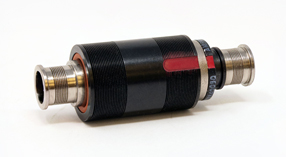
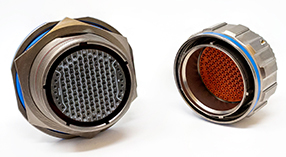
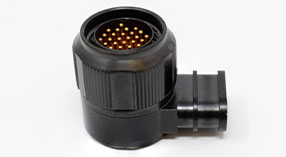
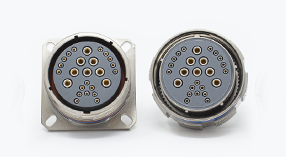
Navigating Harsh Environments in Military and Commercial Aerospace Applications
“Harsh environments" is more than just industry jargon in the defense and commercial air industries — it is a major consideration that shapes the design and functionality of every component used in these applications. Let’s take a closer look at what is meant by "harsh environments" in the context of military and commercial aerospace applications, the attributes that define them, and the mission-critical role of specialized connectors like Amphenol’s 38999 series to ensure reliable performance under these extreme conditions.
Defining Harsh Environments
What Defines a Harsh Environment in Military and Commercial Aerospace Applications?
“Harsh environments” in military and commercial aerospace applications typically refer to environmental and operational conditions that challenge the durability, reliability, and performance of components and systems. These environments are characterized by a combination of severe physical, chemical, and operational stressors that go beyond the normal operational limits of standard equipment.
Key Features of Harsh Environments Include:
Extreme Temperatures:
- Aerospace components often face extreme temperature variations, from the scorching heat near engines or re-entry phases to the frigid cold of high-altitude flights and outer space. Temperatures can range from below -65°C to above 200°C, requiring materials and designs that can withstand such fluctuations without degrading performance.
High Vibration and Shock:
- Military vehicles and aircraft are subjected to intense vibrations and shocks during operation, takeoff, landing, and combat maneuvers. These conditions can cause mechanical fatigue and connector disengagement, meaning robust designs are needed that can endure continuous high-vibration environments.
Corrosive and Humid Conditions:
-
- Exposure to salt spray, humidity, and other corrosive elements is common in aerospace applications, especially for naval and coastal operations. Connectors must resist corrosion to maintain their integrity and functionality over long periods.
Electromagnetic Interference (EMI) and Radio Frequency Interference (RFI):
-
- The presence of high-power electromagnetic fields and radio frequencies can disrupt the performance of electronic systems. Effective EMI/RFI shielding is essential to ensure uninterrupted data transmission and signal integrity.
High Pressure and Vacuum:
-
- Aerospace components must perform reliably under varying pressure conditions, from the high-pressure environments experienced during deep-sea missions to the vacuum of space.
The Need for Harsh Environment Connectors
Given these challenging conditions, the role of connectors optimized to withstand harsh environments is critical. Connectors are the lifeline of electrical systems, enabling the transmission of power, data, and signals. In harsh environments, connectors must not only maintain their electrical performance but also endure the physical and chemical stresses imposed by their surroundings.
Why are Harsh Environment Connectors Vital in Military and Commercial Aerospace Applications?
Reliability and Safety:
-
- In mission-critical applications, the failure of a single connector can lead to catastrophic outcomes. Harsh environment connectors ensure reliable performance, safeguarding both human lives and valuable equipment.
Longevity and Maintenance:
-
- Connectors designed for harsh environments are built to last, reducing the frequency of maintenance and replacements. This longevity translates to lower operational costs and improved system availability.
Operational Efficiency:
-
- Reliable connectors enhance the overall efficiency of aerospace systems, ensuring that communication, navigation, and control systems function without interruption.
Amphenol Connectors are Engineered for Harsh Environments
Amphenol Aerospace connectors are specifically designed to meet the rigorous demands of military and commercial aerospace applications. Our interconnect solutions incorporate extensive ruggedization features that enable them to operate flawlessly in harsh environments:
Ruggedized Shells and Platings:
-
- Amphenol connectors are available with a variety of shell materials and platings, such as stainless steel, aluminum, and composite materials. These materials offer high resistance to corrosion and mechanical damage. Plating options like passivated stainless steel, black zinc nickel, and electroless nickel further enhance their durability and performance in corrosive environments.
Temperature Resilience:
-
- Amphenol connectors are designed to function across a wide temperature range, from -65°C to 200°C. High-temperature versions are also available, making them ideal for applications near engines and other high-heat sources.
Vibration and Shock Resistance:
- Amphenol connectors are available with advanced locking mechanisms and anti-decoupling designs, such as the Dualok system. This ensures that the connectors remain securely mated even under extreme vibration and shock, preventing inadvertent disconnection and maintaining system integrity.
Environmental Sealing:
-
- Amphenol connectors are equipped with robust sealing options, including grommets and seals that provide environmental protection. This ensures that the connectors remain impervious to moisture, dust, and other contaminants, maintaining their performance in adverse conditions.
EMI/RFI Shielding:
-
- To combat electromagnetic and radio frequency interference, Amphenol offers excellent EMI/RFI shielding capabilities for maintaining signal integrity and preventing disruptions throughout any system.
Customizable Configurations:
-
- Amphenol offers a wide range of customization options, including different insert arrangements, contact types, and termination methods to meet any specific application requirement.
Hermetic Sealing:
-
- For applications requiring an airtight seal, such as those in space or underwater environments, Amphenol offers a variety of hermetic configurations to prevent the leakage of gases and fluids and maintain the integrity of the internal system environment.